Exhaust Gas Thermal Recovery in TFT-LCD Plant
SHWave Welded Plate Heat Exchanger Helps Exhaust Gas Thermal Recovery in TFT-LCD Plant
DETAIL
SHWave Welded Plate Heat Exchanger Helps Exhaust Gas Thermal Recovery in TFT-LCD Plant
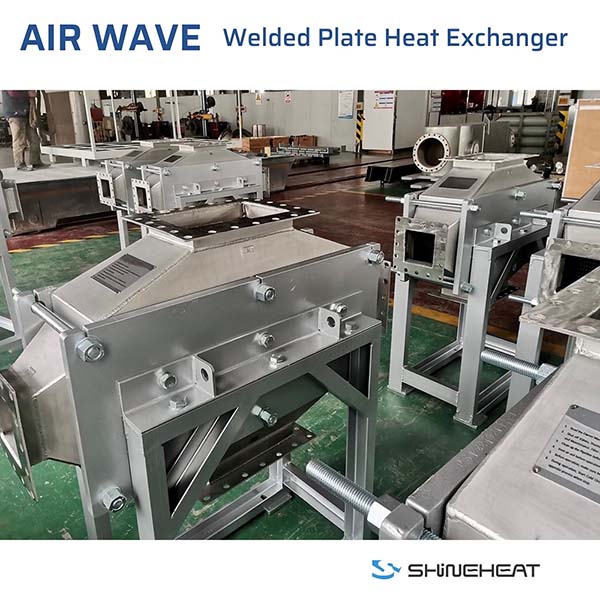
The Background
The Thin Film Transistor-Liquid Crystal Display (TFT-LCD) is widely used in mobile phone, computer, TV, flat panel and other industries in recent years. TFT-LCD production process mainly includes Array, Color Filter (CF), Cell, Module four parts. Array, CF, and Cell are the main links to discharge gas pollutants.
The Job Description:
A furnace is used in the manufacture of liquid crystal display panels. In the furnace, often from the workpiece evaporation gas will contain organic vapor. The vapor may have an adverse effect on the workpiece. Therefore, it is necessary to carry out ventilation in the furnace. But the air change will reduce the temperature inside the furnace. Therefore, there is a need for heat exchange between the exhaust from the furnace and the suction into the furnace.
It is expected to improve the heat recovery efficiency of the heat recovery device which can recover the heat of high temperature gas to heat the low temperature gas. In addition, the manufacturing cost of the heat recovery unit is expected to be controlled.
So, the AIR-Wave offer an optimal solution for thermal recovery device;
As known that Plate Heat Exchanger is very efficient heat exchanger device which widely used for various industries. AIR-Wave is kind of Welded Plate Heat Exchanger which free of Rubble gaskets. Compared with Tube and Shell heat exchanger, it is much more efficient with lower manufacturing cost; Compared with Plate and Gasket Heat Exchanger, it could work under higher temperature which rubber gaskets can’t apply for.
Through AIR-Wave Plate Heat Exchanger,
The Waste Gas from the furnace temperature is 250°C, it is need decrease to blow 80°C before emission, whereas the air temperature for ventilation need to increase to 150 °C before filling into furnace. Now it is time for AIR-Wave to carry out this heat exchanger Job.
Following is Thermal Technical Data and Sheet and Structure Design Drawing by SHINEHEAT TECH.

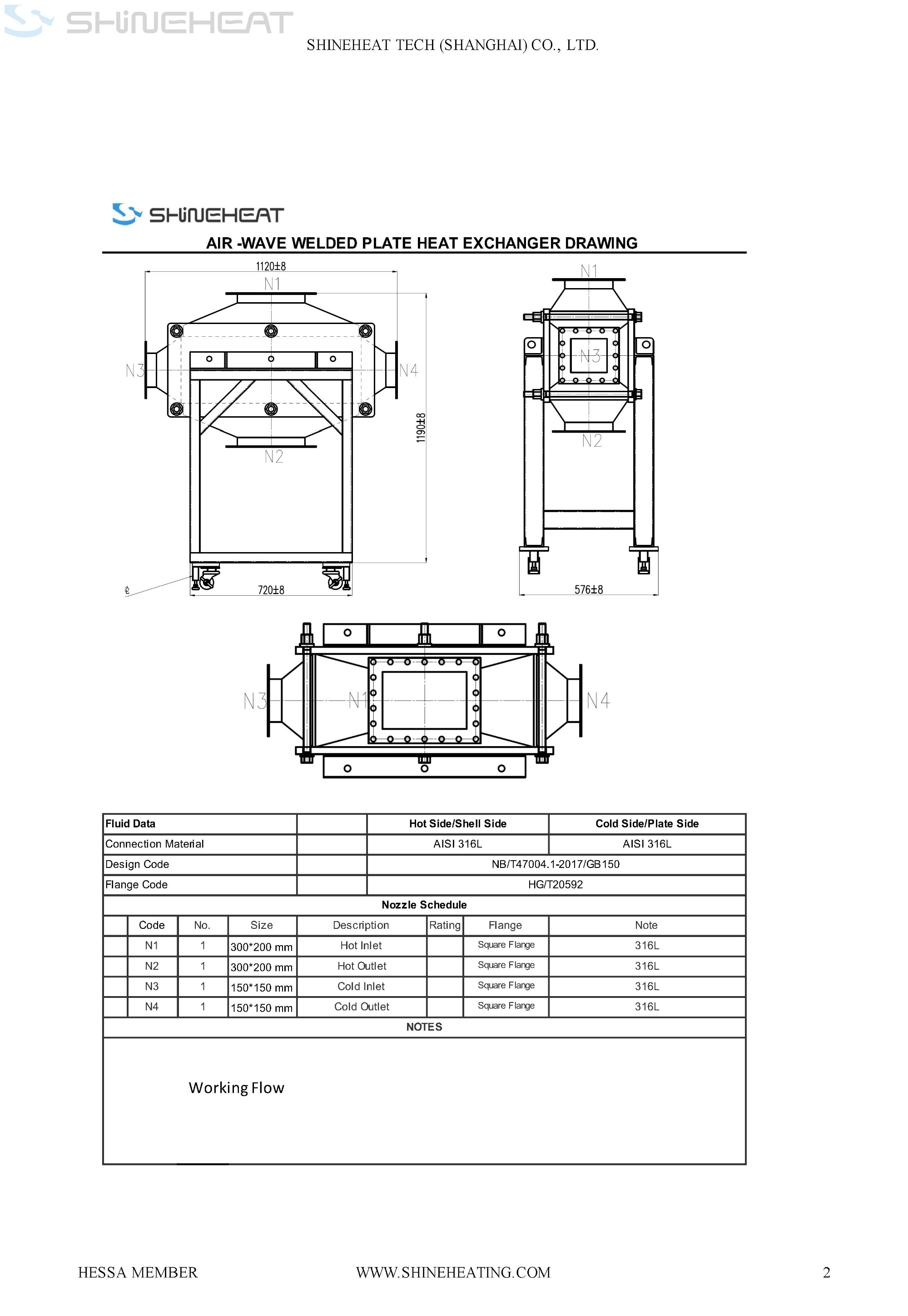
In practical application concerns
The Highlights for Thermal Design for Air Wave Air Cooler
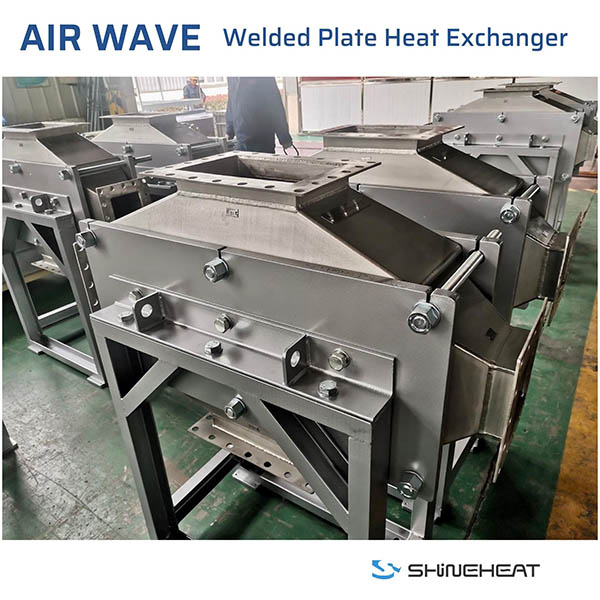
Finally, the Start-Up and Commissioning running is very successfully, especially the Thermal performance is satisfactory.
TAIWAN HESSA supervises the air cooler Start-up and Commissioni
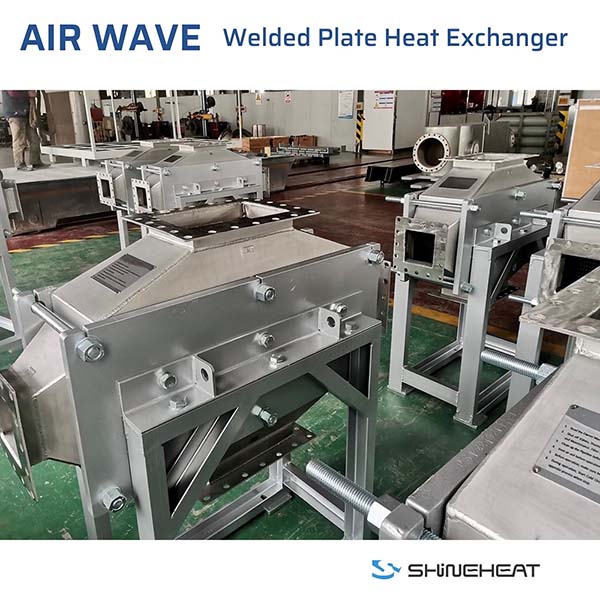
The Background
The Thin Film Transistor-Liquid Crystal Display (TFT-LCD) is widely used in mobile phone, computer, TV, flat panel and other industries in recent years. TFT-LCD production process mainly includes Array, Color Filter (CF), Cell, Module four parts. Array, CF, and Cell are the main links to discharge gas pollutants.
The Job Description:
A furnace is used in the manufacture of liquid crystal display panels. In the furnace, often from the workpiece evaporation gas will contain organic vapor. The vapor may have an adverse effect on the workpiece. Therefore, it is necessary to carry out ventilation in the furnace. But the air change will reduce the temperature inside the furnace. Therefore, there is a need for heat exchange between the exhaust from the furnace and the suction into the furnace.
It is expected to improve the heat recovery efficiency of the heat recovery device which can recover the heat of high temperature gas to heat the low temperature gas. In addition, the manufacturing cost of the heat recovery unit is expected to be controlled.
So, the AIR-Wave offer an optimal solution for thermal recovery device;
As known that Plate Heat Exchanger is very efficient heat exchanger device which widely used for various industries. AIR-Wave is kind of Welded Plate Heat Exchanger which free of Rubble gaskets. Compared with Tube and Shell heat exchanger, it is much more efficient with lower manufacturing cost; Compared with Plate and Gasket Heat Exchanger, it could work under higher temperature which rubber gaskets can’t apply for.
Through AIR-Wave Plate Heat Exchanger,
The Waste Gas from the furnace temperature is 250°C, it is need decrease to blow 80°C before emission, whereas the air temperature for ventilation need to increase to 150 °C before filling into furnace. Now it is time for AIR-Wave to carry out this heat exchanger Job.
Following is Thermal Technical Data and Sheet and Structure Design Drawing by SHINEHEAT TECH.

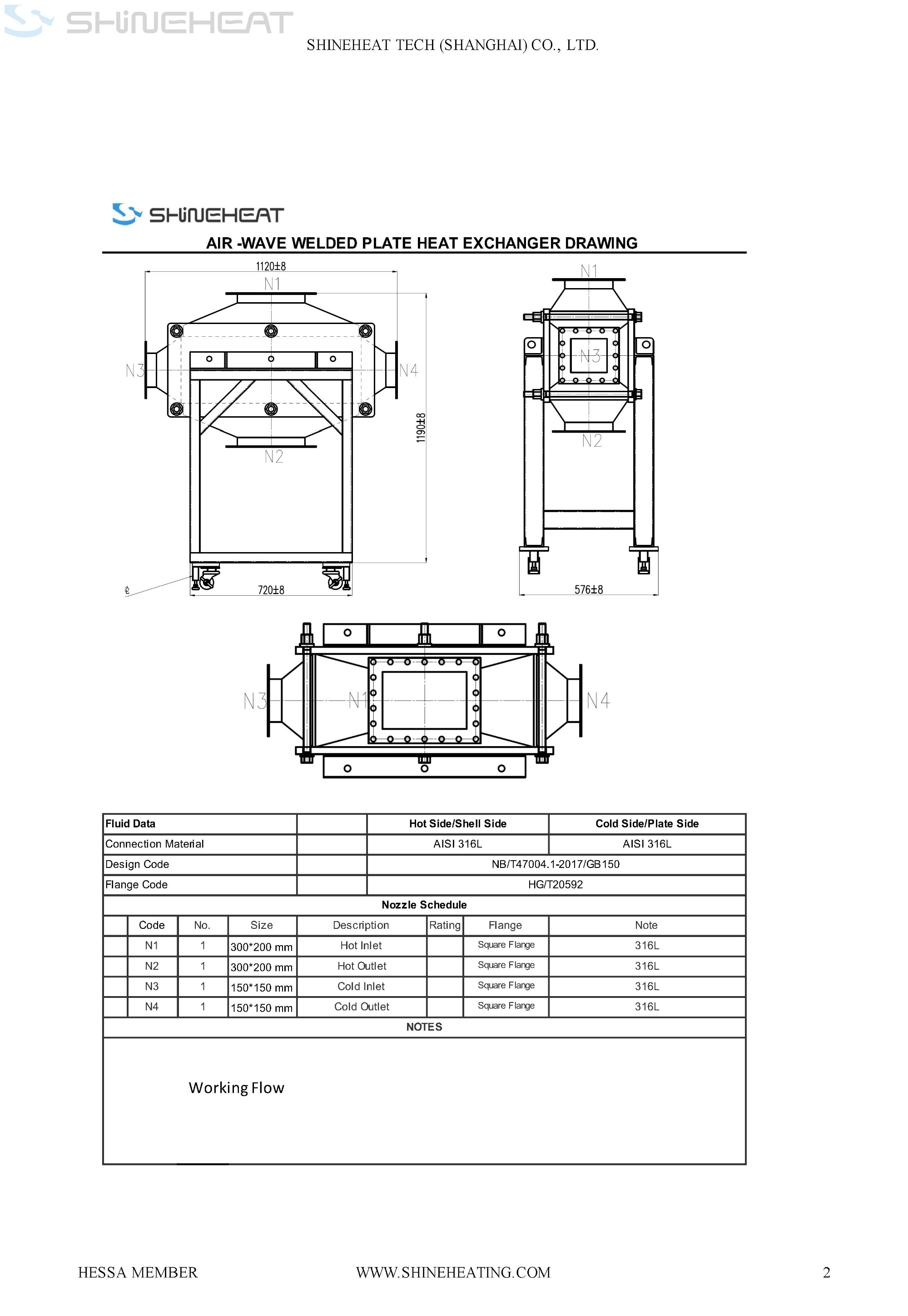
In practical application concerns
- The TFT-LCD Plant is Non-Dust workshop, so the surface treatment will to be High Sanitary Standard.
- In view if space limitation, the Plate Heat Exchanger need to be more compact design.
- Pressure Drop and Thermal Efficient, Shineheat will balance Pd and Q value in comprehensive way, and then select a premium solution;
- Maintenance and Service, Shineheat also took future maintenance and service into design consideration in view of Non-Clean working condition in both sides.
- Modularization Design for future Combined Units working and identically replacement Service
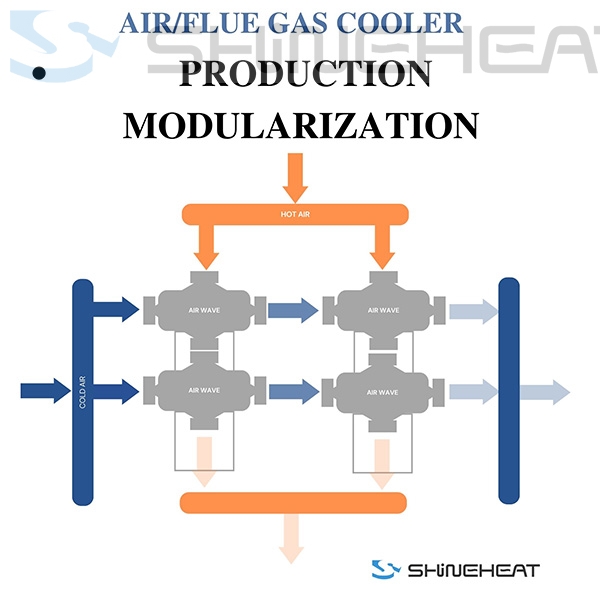
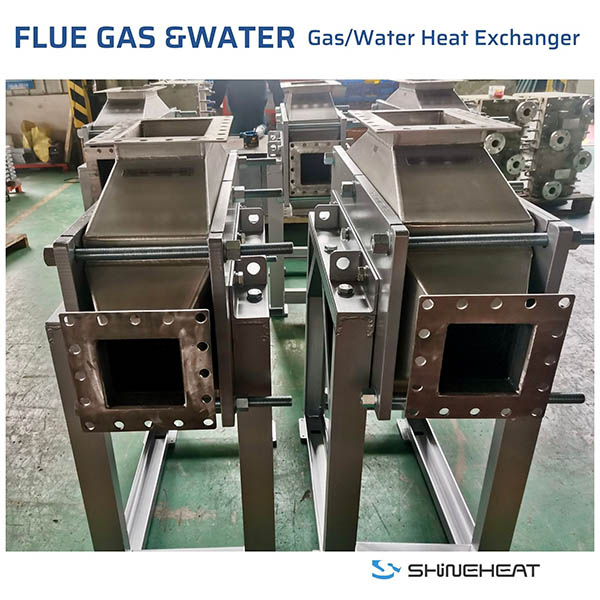
The Highlights for Thermal Design for Air Wave Air Cooler
- Even Distribution for Air Inlet,
- Enough transfer area during transferring process, not “short cut” and “dead spot”
- Separation for condense and air in outlet
- Special design for Universal Wheel foundation, consider the features for Heavy Load-Bearing and Flexible movement.
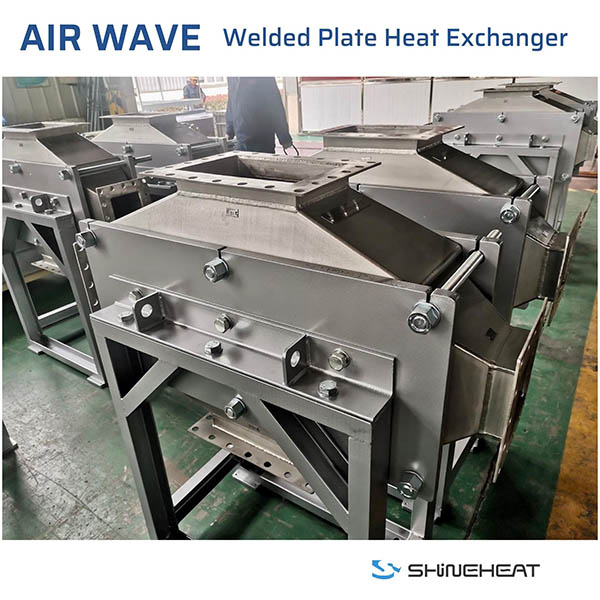
Finally, the Start-Up and Commissioning running is very successfully, especially the Thermal performance is satisfactory.
TAIWAN HESSA supervises the air cooler Start-up and Commissioni